Dynamic Analysis
PROPULSIVE POWER MEASUREMENT
Shaft mechanical power monitoring, integrated with engine parameters, aims to determine the real operating ranges of a ship’s propulsion system, establishing the most suitable working ranges for its operation. The study also makes it possible to identify and adapt the condition of the propulsion system to factory protocols, and to determine any deviations or wear caused by use.
Point Measurement
Through selective data collection during a sea trial navigation, Spot Measurement involves obtaining a status reading from the propulsion system; and/or adjusting equipment after a corrective process, repair, or for power certification needs.
Interval Measurement
It is performed during the vessel’s working period: tide, transits (merchant ships, ferries, etc.). The purpose of this model is to determine and establish the optimal navigation mode (mechanical efficiency vs. consumption management) according to the working model of each vessel.
ARGOS permanent measurement
Continuous monitoring and recording equipment of the navigation and working conditions of a vessel, recording the main parameters of the propulsion system, consumption modes, and auxiliary equipment of the engine room and peripherals.
STUDY PARAMETERS
- Power/torque
- Engine RPM’s
- Consumption
- Speed
- Trajectory
- Rack rate
- Propeller pitch
- Charge air pressure/temperature
- Turbo RPM’s
- Fluid pressure/temperature
- Pressure/Temperature ambient conditions
- Thrust
OBJECTIVES
- Real-time propulsion system analysis
- Consumption modes study
- Post-repair settings check
- Protocol verification
- Establishment of navigation sweet spot
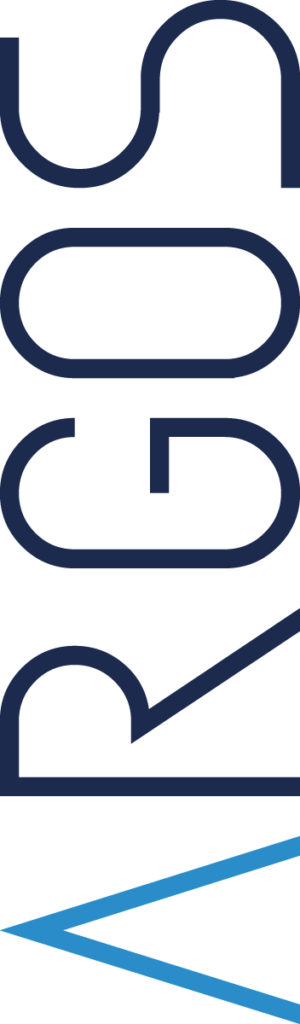
GAS MEASUREMENT
Among the initiatives to control pollutant emissions into the atmosphere regulated by Annex VI of the Marpol Convention (IMO), the requirements and restrictions on specific environmental pollution stand out.
Through IMO, the EIAPP (Engine International Air Pollution Prevention) certificate has been made compulsory for international shipping.
COTERENA provides a procedure for on-board confirmatory test measurements, which complies with chapter 6.3 of the NOx Technical Code 2008, valid for on-board test measurements after conversions or power modifications.
VIBRATION STUDY
Vibration measurement is one of the most effective non-corrective repair tools to determine mechanical equipment internal situations (mainly gearboxes). Its ability to identify components’ wear or deformation while the machine is running allows significant savings before corrective repairs.
COTERENA performs two types of Vibration Studies:
Rotational (polar) vibrations:
Technique based on the study of the torsional vibration trend values, which allows the detection of mechanical faults or failures in any rotating machine, as well as the evaluation of their severity.
Structural (triaxial line) vibrations:
They are mainly used to ensure the comfort of on-board personnel (ISO 6954:2000) by detecting improper vibration levels. In addition, they can be used to assist in the early detection of anomalies in the structure of machinery, hull or cabin components.
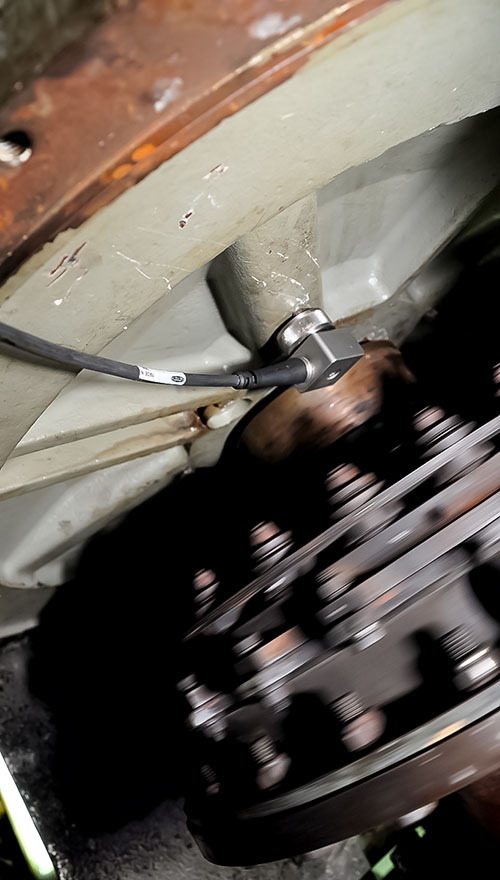
APPLICATIONS
Unbalances, Misalignments, Bearings, Clearances, Rocks, Bent shafts, Lubrication, Gears…
NOISE ANALYSIS
Noise as a safety factor in the workplace becomes an important aspect in a ship. The acoustic analyses performed on board make it possible to determine the acoustic quality of cabins, engine rooms and living or working spaces.
For the implementation of noise control protocols, IMO MSC 91/22/Add1 is used as a reference and Resolution A.343 (IX) of the Inter-Governmental Maritime Consultative Organization is adopted as a procedure for the noise measurements implementation.
PROCESS MONITORING
The Process Monitoring performed by COTERENA is mainly focused on preventive adjustment techniques and on the anomaly detection in hydraulic systems (clutches, brakes) or pneumatic systems (controls, electro-pneumatic systems…).
Monitoring capacity, even at high recording speeds, makes it possible to study the evolution over time of different parameters, as well as their relationship with other processes for the detection of synchronisation failures and incorrect adjustments in clutch processes, control equipment, etc… Providing measurement sensors for:
- Pressure
- Flow
- Temperature
- Rotation speed
- Accelerometers
- Magnetometers
- Customer-integrated sensor signals through galvanic isolators
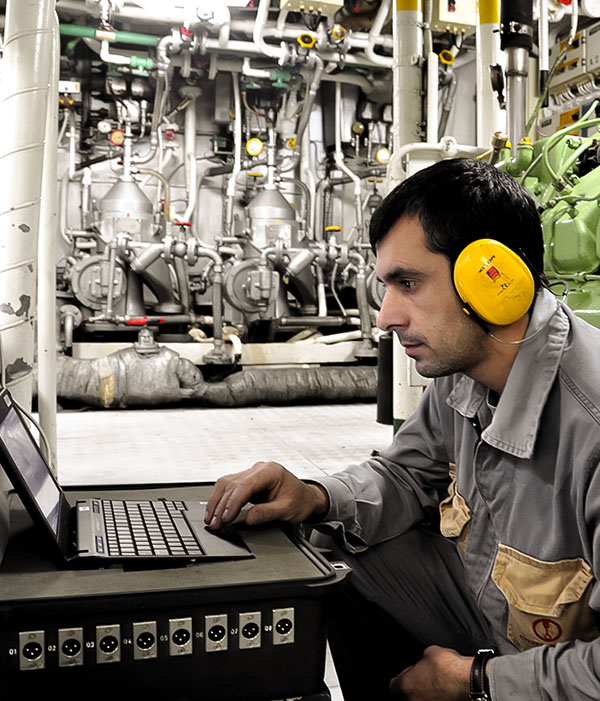
INDUSTRIAL VIDEOSCOPY
The endoscopic cameras used to study possible incidents or breakdowns in areas that are difficult to access visually or tactilely allow significant cost savings when determining whether or not a disassembly is necessary, with the consequent corrective process.
Video or photographic documentation using endoscopic techniques can also serve as a guarantee for insurers or companies when determining the need for a corrective repair, allowing them to plan and reduce both the economic burden of the repair process and the necessary time to identify and locate the fault.
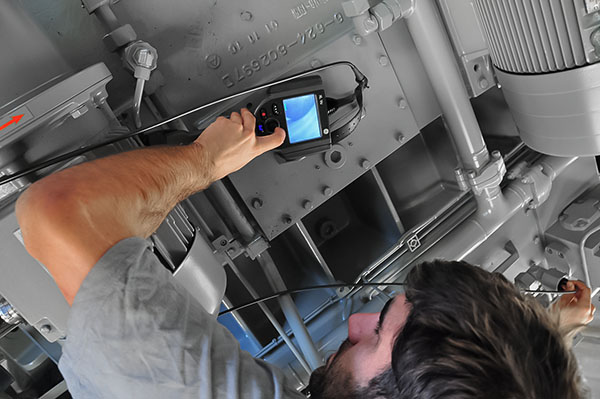